چرا ریخته گری فولاد حائز اهمیت است؟
در دنیای صنعت، فولاد حرف اول را می زند. استحکام، پایداری و انعطاف پذیری این فلز، آن را به ماده ای بی نظیر برای ساخت تجهیزات و قطعات مختلف تبدیل کرده است؛ اما چگونه می توان فولاد را به اشکال و ابعاد دلخواه درآورد؟ پاسخ در فرآیندی شگفت انگیز به نام «ریخته گری فولاد» نهفته است. ریخته گری یکی از قدیمی ترین روش های شکل دهی به فلزات است که در آن مواد مذاب را درون قالب هایی با شکل دلخواه ریخته و پس از سرد شدن، آنها را منجمد می کنند. این روش از حدود ۷۰۰۰ سال پیش مورد استفاده قرار گرفته است. در این مقاله پس از شرح مختصر انواع ریخته گری فولاد به ریخته گری پیوسته شمش که به دلیل کیفیت بالا و کاهش هزینه ها، برای تولیدات انبوه ایده آل است، می پردازیم.
روش های ریخته گری فولاد
به طور کلی می توان ریخته گری فولاد را به دو دسته قطعه ریزی (برای تولید قطعات مانند چرخ دنده، شافت، غلتک، شاتون) و شمش ریزی (بلوم، بیلت، اسلب) تقسیم کرد.
شمش فولادی؛ مقایسه با اسلب، بیلت و بلوم
شمش ریزی
ریخته گری شمش فولادی به روش های مختلفی متناسب با نیاز صنعتگران انجام می شود. در ادامه مقاله ریخته گری فولاد، نکات تکمیلی و جزئیات بیشتری درباره مراحل، مزایا، معایب و کاربردهای ریخته گری فولاد ارائه شده است.
آهن اسفنجی | رمز تولید فولاد باکیفیت
در این روش، مواد مذاب درون قالب های مخصوصی ریخته می شوند تا پس از انجماد، شمش مورد نظر به دست آیند. ریخته گری شمش فولاد به دو دسته کلی ریخته گری تکباری (ingot) و ریخته گری پیوسته (continuous) تقسیم می شود.
- ریخته گری تکبار: در این روش، مواد مذاب درون قالب هایی از جنس چدن که از داخل با جریان آب خنک می شوند ریخته می شود. امروزه این روش بیشتر برای فلزات غیرآهنی کاربرد دارد. این روش در گذشته برای تولید بیلت های فولادی نیز به کار می رفت ولی به دلیل مشکلاتی مانند حفرات گازی و حفرات ریختگی، و یکنواخت نبودن ساختار متالورژیکی شمش، کنار گذاشته شد. تنها کاربرد فعلی این روش، تولید شمش (بیلت، بلوم، اسلب) برای فولادهای جوشان است.
- ریخته گری پیوسته: در این روش، فرآیند تولید پیوسته بوده و خروجی شامل شمشال (بیلت)، شمشه (بلوم) و تختال(اسلب)هایی است که به عنوان مواد اولیه در صنایع دیگر استفاده می شوند. این روش به دلیل کیفیت بالا و کاهش هزینه ها، برای تولیدات انبوه ایده آل است.
قطعه ریزی
در این روش، قطعات با شکل نهایی مورد نظر تولید می شوند و به سه دسته کلی تقسیم می شوند: قالب های دائمی، قالب های موقت و قالب های مصرف شونده.
ریخته گری پیوسته شمش چیست؟
ریخته گری پیوسته شمش یکی از مهم ترین و پرکاربردترین فرآیندهای تولید در صنایع فلزی به شمار می رود که به منظور تبدیل فلزات مذاب به محصولات نیمه نهایی مانند شمش، بیلت و تختال مورد استفاده قرار می گیرد. این روش، به دلیل پیوستگی و بازدهی بالا، نقش قابل توجهی در افزایش بهره وری، کاهش هدررفت انرژی و ارتقای کیفیت محصولات نهایی ایفا می کند.
در این فرآیند، فلزات مذاب از مرحله ذوب تا انجماد و شکل گیری نهایی به صورت کاملاً پیوسته و تحت کنترل دقیق دما، حرکت و سرعت انجماد، به محصولات فلزی تبدیل می شوند. محصولات حاصل از این نوع ریخته گری، به عنوان مواد اولیه در واحدهای نورد، کشش و سایر عملیات مکانیکی برای تولید مقاطع فولادی مانند میلگرد و کلاف استفاده می شوند.
مراحل فرآیند ریخته گری پیوسته شمش
ذخیره و آمادهسازی فلز مذاب. در نخستین گام، فلز مذاب درون کوره ذوب شده و سپس برای دستیابی به خواص مورد نظر، عملیاتی نظیر گاززدایی، تنظیم ترکیب آلیاژی و رساندن به دمای بهینه صورت می گیرد. پس از آماده سازی، مذاب به مخزن ذخیره منتقل می شود.
انتقال مذاب به تاندیش. فلز مذاب از مخزن به مخزن میانی ثابتی به نام تاندیش منتقل می شود. تاندیش نقشی کلیدی در تنظیم پیوستگی جریان مذاب، کنترل دما و مقدار جریان دارد. این مخزن به گونهای طراحی شده که بتواند در هنگام تعویض منبع تغذیه، جریان مذاب را بدون توقف حفظ کند.
سرمایش اولیه در قالب مسی. مذاب از تاندیش به درون قالب های مسی با دیواره های خنک شونده با آب هدایت می شود. در این قالب، سرمایش اولیه فلز و شکل دهی ابتدایی مقطع صورت می گیرد. حرکت نوسانی قالب از چسبیدن مذاب به دیواره ها جلوگیری می کند و لایه ای از فلز منجمد شده (استرند) در تماس با دیواره قالب شکل می گیرد.
تشکیل لایه استرند و انجماد جزئی. در اطراف قالب، لایه ای از فلز منجمد (استرند) شکل می گیرد، در حالی که هسته مرکزی هنوز مذاب است. برای حفظ شکل این لایه، استرند وارد ناحیه ای با ریل ها و غلتک های پشتیبان شده و همزمان توسط افشانک هایی با آب خنک می شود تا انجماد به صورت یکنواخت پیش رود.
سرمایش ثانویه. پس از خروج از قالب، شمش نیمه جامد وارد منطقه خنک سازی ثانویه می شود. در این منطقه، جریان آب پرفشار از طریق نازل ها به صورت پودر روی سطح شمش پاشیده شده و فرآیند انجماد را تا مرکز شمش ادامه می دهد. مصرف آب در این مرحله بین ۰.۵ تا ۰.۸ مترمکعب به ازای هر تن فولاد است.
شکل دهی نهایی و خروج محصول. شمش پس از انجماد کامل، از میان غلتک هایی عبور داده می شود که وظیفه هدایت، تنظیم ابعاد و تغییر جهت حرکت آن از عمودی به افقی را بر عهده دارند. در نهایت، مقاطع تولیدی به طول مورد نظر بریده شده و برای فرآیندهای بعدی آماده سازی می شوند.
عملیات پس از ریخته گری
محصولات به دست آمده از فرآیند ریخته گری پیوسته، به عنوان مواد نیمه آماده وارد بخش هایی نظیر نورد، مفتول کشی و عملیات مکانیکی دیگر می شوند. بسیاری از واحدهای تولیدی، این عملیات را به صورت پیوسته و بلافاصله پس از ریخته گری انجام می دهند تا از دمای باقی مانده در شمش ها استفاده کرده و در مصرف انرژی صرفه جویی کنند.
نورد گرم و سرد: راز استحکام فلزات، کاربرد، مزایا و معایب
انواع روش های ریخته گری پیوسته شمش
همان طور که پیش از این گفته شد، این نوع ریخته گری یکی از روش های متداول و کارآمد برای تولید شمش های فلزی است که در آن فلز مذاب به صورت مداوم در قالب ریخته شده و به تدریج منجمد می شود. این فرآیند بسته به جهت حرکت شمش، نوع قالب و نحوه خنک سازی و برش، به انواع مختلفی تقسیم می شود. در ادامه، مهم ترین روش های این نوع ریخته گری شمش معرفی شده اند:
- Continuous Casting عمودی با خنکسازی و برش در همان راستای عمودی
- Continuous Casting عمودی با خمش و برش در راستای افقی
- Continuous Casting خمیده با انجماد در قالب منحنی با شعاع ثابت یا متغیر و برش افقی
اصول و الزامات فنی ریخته گری پیوسته
در تمام روش های این نوع ریخته گری، اصول کلی فرآیند مشابه است. فولاد مذاب به طور پیوسته از پاتیل به تاندیش و سپس به قالب منتقل می شود. قالب ها معمولاً از جنس مس و مجهز به سیستم خنک کننده آبگرد هستند. برای جلوگیری از چسبندگی شمش به دیواره قالب، قالب ها با حرکت نوسانی کنترل شده ای عمل می کنند. در ادامه، انجماد از دیواره ها به سمت مرکز شمش پیش می رود.
برای خنک سازی مؤثر، در مرحله اول حدود ۵ تا ۲۰ مترمکعب آب با فشار ۰.۶ مگاپاسکال به ازای هر تن فولاد مصرف می شود. در ناحیه خنک سازی ثانویه، فشار آب پاششی حدود ۰.۲ تا ۰.۳ مگاپاسکال بوده و با مصرف کمتر از یک مترمکعب آب، انجماد کامل شمش تضمین می شود.
استانداردهای ریخته گری فولاد
در صنعت ریخته گری فولاد، استانداردهای متعددی برای تضمین کیفیت و ایمنی مورد استفاده قرار می گیرند، از جمله:
- استانداردهای بینالمللی ISO 4990، ISO 3755
- استانداردهای آمریکایی ASTM A216، ASTM A352
- استانداردهای اروپایی EN 10293، EN 10213
- استانداردهای ملی ایران INSO 20300 ، INSO 5426
- استانداردهای آلمان DIN 1681، DIN 1686
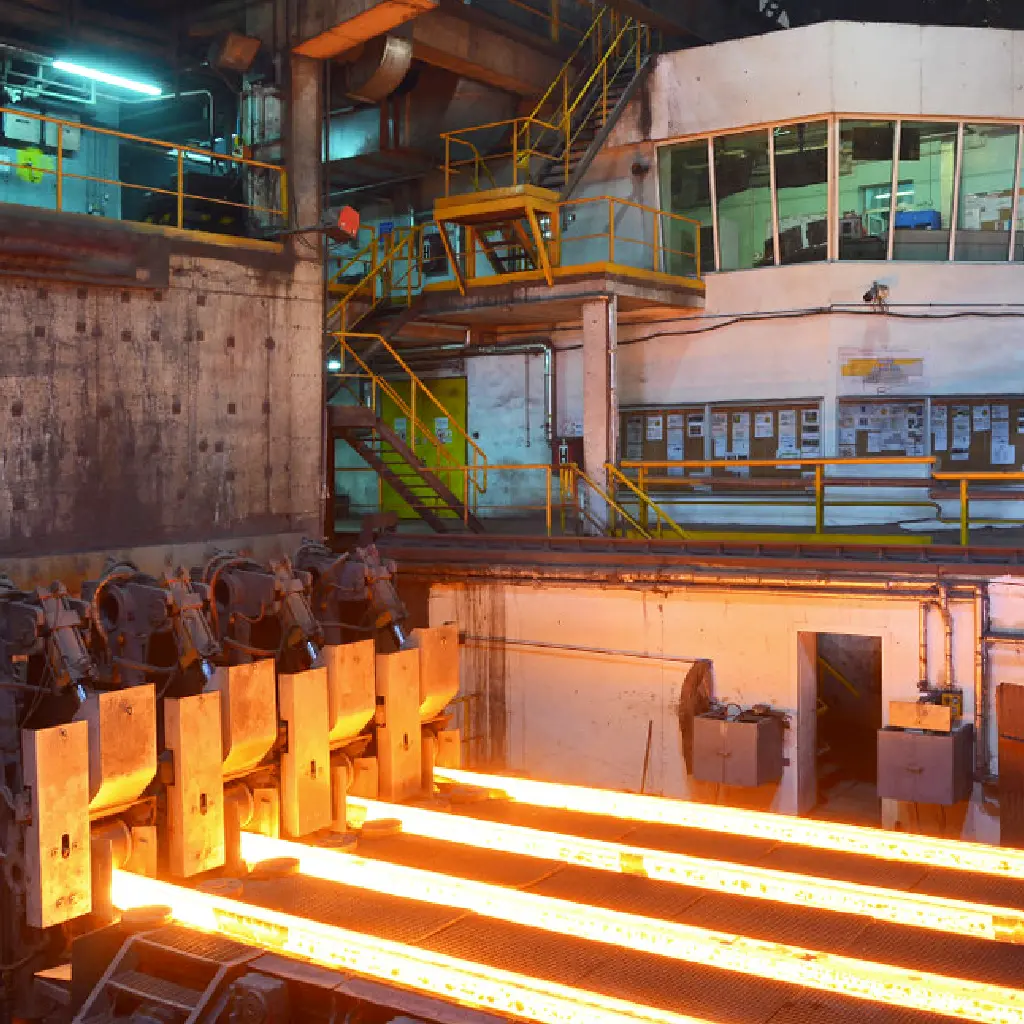
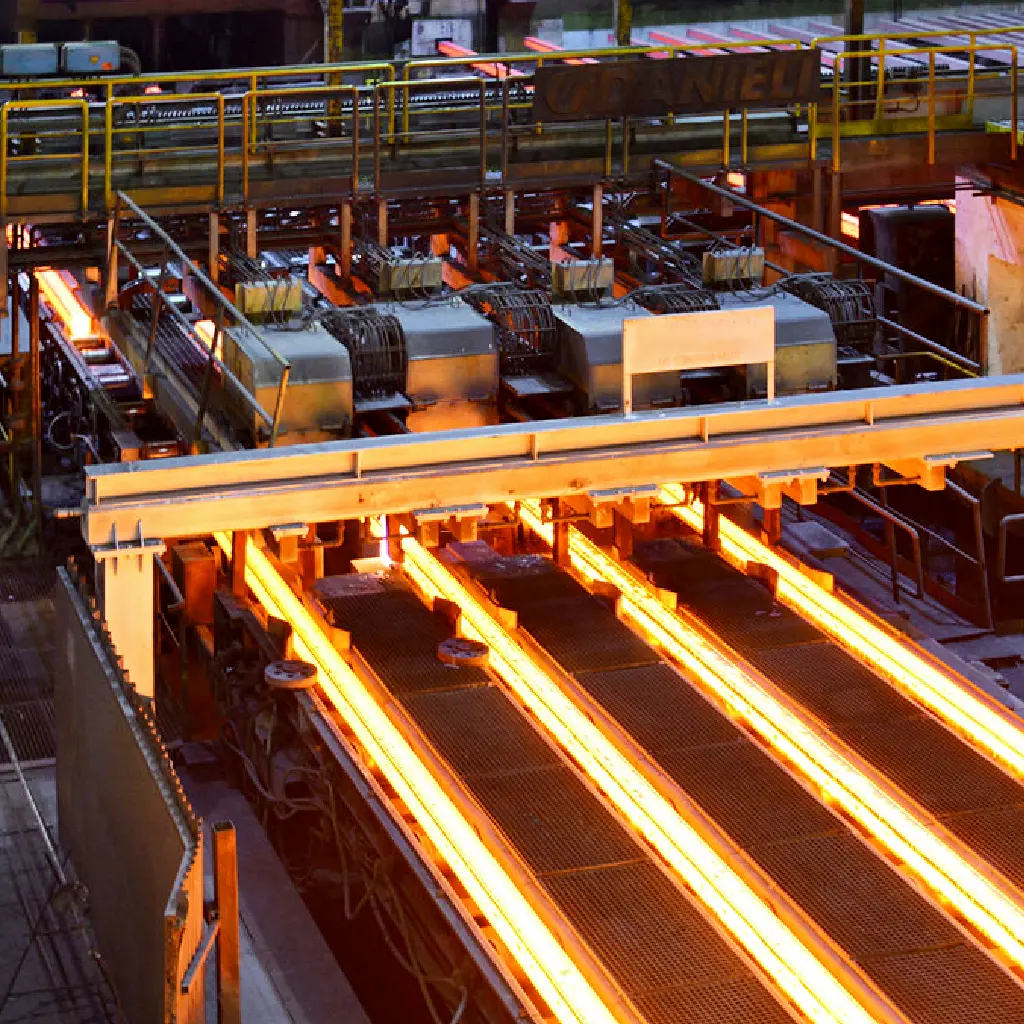
کلام پایانی
ریخته گری پیوسته شمش، فرآیندی کلیدی در صنعت فولاد است که به واسطه ویژگی هایی چون صرفه جویی در انرژی، افزایش بهره وری، کیفیت یکنواخت و پیوستگی تولید، جایگاه مهمی در خطوط تولید کارخانه ها دارد. این فرآیند نه تنها امکان تولید شمش های متنوع با ابعاد مختلف را فراهم می کند، بلکه با اتصال به خطوط نورد، موجب تسهیل و تسریع عملیات تولید محصولات نهایی نیز می شود. برای آشنایی با کلیه واحدهای تولیدی مجتمع فولاد بافق، از جمله واحد فولادسازی، به لینک زیر رجوع کنید.